How Appropriate Cutting Tools Can Improve Your Production Efficiency?
- Mark Smith
- Jan 9, 2024
- 4 min read
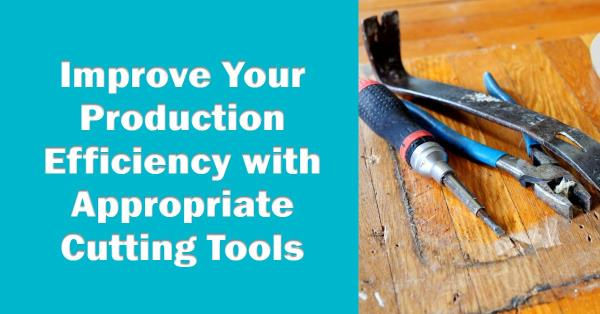
In the dynamic landscape of modern manufacturing, optimising production efficiency is paramount. One often overlooked but crucial aspect of this optimisation lies in the selection. This aspect is especially pertinent in industries where precision is a non-negotiable benchmark. The choice of cutting tools extends far beyond a mere technical decision. It impacts a company's bottom line.
In this exploration, we delve into the pivotal role that cutting tools play. The right tools can reduce production times and elevate the total output quality. This discussion will navigate through the intricacies of selecting cutting tools. We will uncover how investing in the right cutting tools can make substantial gains.
Join us on this insightful journey. Moreover, the rapid advancements in technology have given rise to a plethora of cutting tool innovations. From carbide end mills optimising precision to diamond-tipped blades revolutionising cutting, the options are vast. We will explore case studies and success stories from various industries.
Efficiency gains are just a few of the compelling outcomes. The discussion will extend beyond tool selection to encompass maintenance practices. We aim to empower manufacturers, engineers, and production managers with the knowledge needed. This exploration serves as a guide for companies aspiring to meet industry standards.
The Diversity of Cutting Tools
In the realm of manufacturing, choosing the right cutting tools is pivotal. A cutting tools manufacturer understands the diverse needs of industries. The selection process involves assessing factors such as material type and production volume. Hydraulic cutters find prominence in tasks requiring high force and precision.
Versatility, efficiency, and durability distinguish cutting tools, ensuring optimal performance across various applications. As industries evolve, innovative materials and designs enrich the repertoire of cutting tools. Discerning manufacturers recognise the importance of staying abreast of these advancements. The diversity of cutting tools remains a cornerstone for achieving precision and productivity.
This variety extends beyond traditional choices, embracing advancements like carbide end mills and diamond-tipped blades. Manufacturers must explore these options, aligning their selection with specific tasks and materials. Moreover, technological innovations propel the evolution of cutting tools, introducing smart features that further amplify efficiency.
Transitioning from conventional to advanced cutting tools necessitates informed decision-making.
Collaborating with a cutting tools manufacturer ensures access to expertise and tailored solutions. The transformative impact of hydraulic cutters becomes apparent in tasks demanding both power and finesse. In navigating this diversity, industries unlock a spectrum of benefits. As manufacturers embrace the ever-expanding array of cutting tools, they position themselves at the forefront.
The Landscape of Modern Manufacturing
In modern manufacturing, a cutting tools manufacturer plays a pivotal role. Industries, propelled by technological advancements, face relentless challenges. From precision CNC machining to robust metal fabrication, the demand for efficiency remains paramount. Amidst this complexity, hydraulic pumps emerge as crucial components, providing the necessary force. Transitioning from conventional methods to advanced technologies necessitates strategic adaptation.
Industries embracing this evolution gain a competitive edge in the global market. As innovation shapes the manufacturing narrative, the role of tool manufacturers becomes even more pivotal. They offer not just tools but expertise, guiding businesses towards optimal solutions. In this landscape, staying ahead involves a holistic approach. The synthesis of these elements defines the modern manufacturing ecosystem.
Navigating this terrain needs a strategic partnership with cutting tools manufacturers. This symbiotic relationship extends beyond tools and machinery. A forward-looking approach involves embracing the latest equipment. The integration of cutting tools and hydraulic pumps exemplifies this synergy.
Businesses that adapt and invest in these advancements position themselves as industry leaders. Furthermore, collaboration with tool manufacturers becomes a strategic imperative. Beyond supplying tools, these experts serve as partners in progress, offering insights into evolving industry trends. In this dynamic landscape, the role of a manufacturer becomes a guiding force.
Factors Influencing Tool Selection and Performance
When selecting tools, a cutting tools manufacturer guides choices for optimal performance. Factors like material compatibility and tool lifespan play a crucial role in decision-making. Transitioning from conventional to advanced cutting tools demands a strategic approach for success. In precision industries, such as those using aluminium connectors, the right tools influence efficiency.
Here are key considerations for selecting cutting tools:
Material compatibility: Choose tools aligned with the specific material needs of your task.
Production volume: Match tool capacity with production demands to avoid bottlenecks or inefficiencies.
Tool lifespan: Consider the durability of tools to optimise performance and minimise downtime.
Cost-effectiveness: Balance the cost of tools with their performance to maximise the value.
As industries evolve, staying informed about new materials and designs is important. Collaborating with knowledgeable cutting tools manufacturers ensures businesses align their operations. The synergy between manufacturers and cutting tools becomes the cornerstone of efficiency. In addition to these considerations, the versatility of cutting tools should be evaluated.
Opt for tools that can adapt to various tasks within your manufacturing processes. Moreover, understanding the specific needs of your industry is crucial. For instance, industries relying on aluminium connectors may need tools tailored to the unique characteristics of this material. Transitional technologies are also significant factors.
Conclusion
In conclusion, the symbiotic relationship between manufacturers and cutting tools remains integral. The diversity of cutting tools plays a pivotal role in achieving precision. As industries embrace this ever-expanding array of tools, they position themselves at the forefront of efficiency. Collaborating with cutting tools manufacturers ensures access to expertise, guiding businesses towards optimal solutions.
The integration of cutting tools and hydraulic pumps exemplifies the synergy driving industry leaders. Beyond copper connectors, the evolving needs of industries demand a strategic partnership to carve paths. Transitional technologies and smart features further amplify the efficiency gains.
Comentarios